La maintenance en condition opérationnelle (MCO) constitue un enjeu majeur pour les entreprises industrielles et les organismes de défense. Cette approche vise à garantir la disponibilité et la fiabilité des équipements tout au long de leur cycle de vie. Le MCO regroupe l'ensemble des opérations nécessaires au maintien des performances des systèmes, qu'il s'agisse de véhicules, d'aéronefs ou d'infrastructures critiques. En intégrant des processus préventifs et correctifs, le MCO permet d'optimiser les coûts tout en préservant la capacité opérationnelle des matériels. Son importance s'est accrue ces dernières années, notamment dans le secteur de la défense où les contraintes budgétaires et opérationnelles sont fortes. Découvrons les principaux avantages qu'offre la mise en place d'une stratégie de maintenance en condition opérationnelle.
Réduction des coûts de maintenance opérationnelle
La mise en œuvre d'une démarche de maintenance en condition opérationnelle permet de réaliser des économies substantielles sur le long terme. En effet, le MCO repose sur une approche préventive et prédictive qui vise à anticiper les défaillances avant qu'elles ne surviennent. Cette anticipation permet de planifier les interventions de maintenance de manière optimale, réduisant ainsi les arrêts imprévus et les réparations d'urgence souvent plus coûteuses. De plus, le suivi régulier des équipements dans le cadre du MCO favorise une meilleure gestion des stocks de pièces détachées. Les entreprises peuvent ainsi éviter les ruptures de stock tout en limitant les surstockages onéreux. La rationalisation des processus de maintenance induite par le MCO permet également d'optimiser l'utilisation des ressources humaines et matérielles dédiées à l'entretien des équipements. Cette optimisation se traduit par une réduction des heures de main-d'œuvre et une meilleure allocation des compétences techniques.
L'analyse des données collectées dans le cadre du MCO, telle proposée par novae-group.com, offre par ailleurs de précieuses informations pour identifier les composants les plus sujets aux pannes et orienter les investissements vers des équipements plus fiables. Cette approche data-driven contribue à réduire les coûts de maintenance sur le long terme en ciblant les points faibles des systèmes. Enfin, en prolongeant la durée de vie des équipements grâce à un entretien régulier et adapté, le MCO permet de repousser les investissements lourds liés au renouvellement des matériels. Cette optimisation du cycle de vie des actifs industriels représente une source d'économies non négligeable pour les entreprises, en particulier dans les secteurs nécessitant des équipements coûteux comme l'aéronautique ou la défense.
Optimisation de la disponibilité des équipements
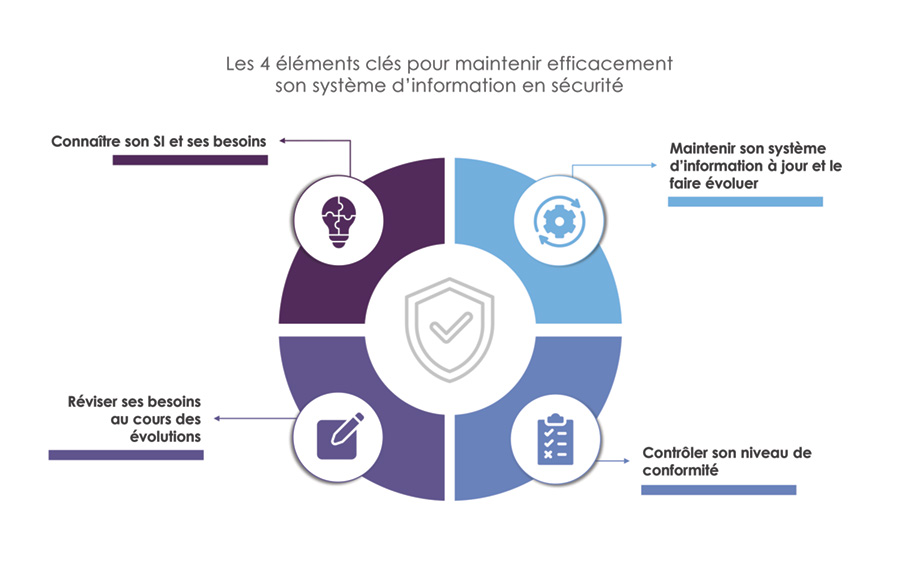
L'un des objectifs principaux de la maintenance en condition opérationnelle est de maximiser la disponibilité des équipements critiques. Cette approche globale de la maintenance permet d'améliorer significativement les taux de disponibilité opérationnelle, un indicateur clé de performance pour de nombreuses industries. Le MCO s'appuie sur une combinaison de techniques et de processus visant à réduire les temps d'arrêt tout en garantissant la fiabilité des systèmes. Examinons plus en détail les différents leviers d'optimisation de la disponibilité des équipements dans le cadre d'une démarche MCO.
Planification efficace des interventions de maintenance
La planification des opérations de maintenance constitue un pilier central du MCO. Grâce à l'analyse des données historiques et à l'utilisation d'outils de gestion de maintenance assistée par ordinateur (GMAO), les entreprises peuvent élaborer des plans de maintenance préventive adaptés à chaque équipement. Cette planification fine permet d'intervenir au moment le plus opportun, en tenant compte des contraintes de production et des cycles d'utilisation des matériels. Les arrêts programmés pour maintenance peuvent ainsi être optimisés pour minimiser leur impact sur l'activité opérationnelle. La coordination entre les différents services (production, maintenance, logistique) est également facilitée par cette planification centralisée, réduisant les risques de conflits de planning ou de retards dans les interventions.
Identification précoce des défaillances potentielles
Les techniques de maintenance prédictive intégrées au MCO permettent de détecter les signes précurseurs de défaillances avant qu'elles ne se produisent. L'utilisation de capteurs et d'outils d'analyse avancés (vibrations, thermographie, analyse d'huile) offre une visibilité en temps réel sur l'état des équipements. Ces données sont traitées par des algorithmes sophistiqués capables d'identifier des tendances et des anomalies imperceptibles à l'œil humain. Cette approche prédictive permet d'anticiper les pannes et de programmer les interventions de manière proactive, évitant ainsi les arrêts non planifiés. La maintenance prédictive contribue également à optimiser la durée de vie des composants en intervenant au moment le plus opportun, ni trop tôt ni trop tard.
Diminution des temps d'arrêt imprévus
La réduction des temps d'arrêt non planifiés constitue un avantage majeur du MCO. En combinant maintenance préventive et prédictive, cette approche permet de limiter drastiquement les pannes inopinées qui perturbent la production et engendrent des coûts importants. Lorsqu'une intervention est nécessaire, la préparation en amont (pièces détachées, outillage, documentation technique) permet de minimiser la durée d'immobilisation des équipements. Les équipes de maintenance disposent ainsi de toutes les ressources nécessaires pour intervenir rapidement et efficacement. Par ailleurs, la standardisation des procédures de maintenance dans le cadre du MCO contribue à réduire les erreurs humaines et à accélérer les interventions. Cette optimisation des processus se traduit par une diminution globale des temps d'arrêt, qu'ils soient planifiés ou imprévus.
Amélioration de la sécurité des opérateurs
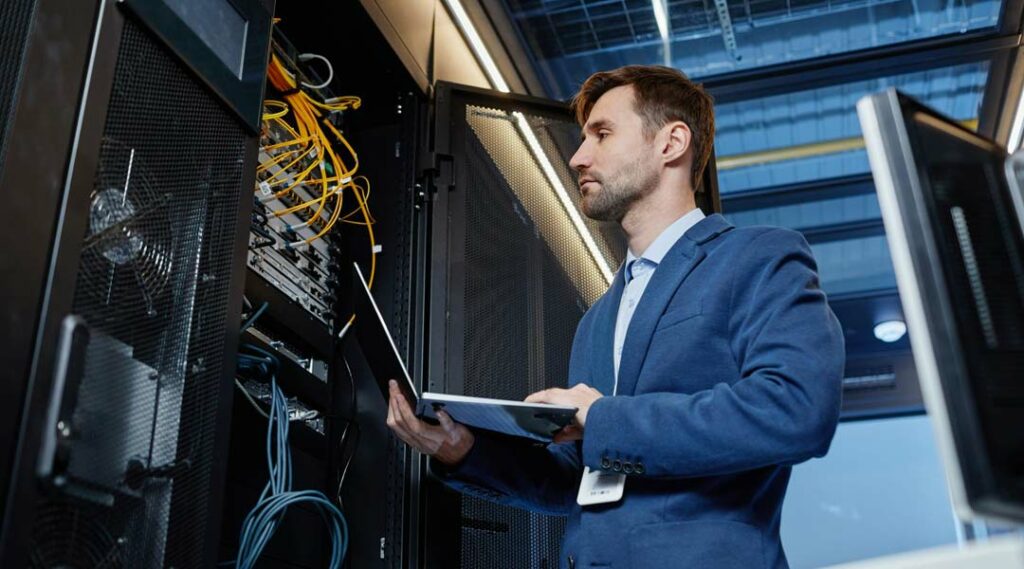
La maintenance en condition opérationnelle joue un rôle crucial dans l'amélioration de la sécurité des personnels travaillant sur les équipements industriels. En effet, un matériel correctement entretenu présente moins de risques de dysfonctionnements pouvant mettre en danger les opérateurs. Le suivi régulier de l'état des machines permet d'identifier et de corriger rapidement les anomalies susceptibles de provoquer des accidents. Les inspections systématiques réalisées dans le cadre du MCO contribuent à maintenir les dispositifs de sécurité en parfait état de fonctionnement, qu'il s'agisse de systèmes d'arrêt d'urgence, de capteurs de présence ou de protections mécaniques. La documentation technique associée au MCO fournit par ailleurs aux opérateurs des informations précises sur les procédures d'utilisation et les précautions à prendre, renforçant ainsi la culture de sécurité au sein de l'entreprise.
Le MCO favorise également une meilleure ergonomie des postes de travail en veillant au bon réglage des équipements et à la réduction des vibrations ou des émissions sonores excessives. Cette approche globale de la maintenance prend en compte les aspects liés à la santé des opérateurs sur le long terme, contribuant ainsi à prévenir les troubles musculo-squelettiques et autres pathologies professionnelles. En outre, la formation continue des personnels de maintenance, partie intégrante du MCO, permet de développer les compétences techniques nécessaires pour intervenir en toute sécurité sur des équipements complexes. Cette montée en compétences réduit les risques d'erreurs lors des interventions et améliore la qualité globale de la maintenance. Enfin, l'analyse systématique des incidents et des presqu'accidents dans le cadre du MCO permet d'identifier les points d'amélioration en matière de sécurité et de mettre en place des actions correctives ciblées.
Prolongation de la durée de vie des équipements
L'un des avantages majeurs de la maintenance en condition opérationnelle réside dans sa capacité à prolonger significativement la durée de vie des équipements industriels. Cette approche globale de la maintenance permet d'optimiser le cycle de vie des actifs, retardant ainsi les investissements lourds liés au renouvellement des matériels. Le MCO s'appuie sur différents leviers pour maximiser la longévité des équipements tout en préservant leurs performances opérationnelles. Examinons plus en détail les mécanismes par lesquels le MCO contribue à étendre la durée de vie utile des installations industrielles.
Suivi régulier de l'état des machines
Le MCO repose sur un suivi continu et méthodique de l'état des équipements. Des inspections régulières, couplées à l'utilisation de technologies de surveillance avancées (capteurs, analyses vibratoires, thermographie), permettent de détecter précocement les signes d'usure ou de dégradation. Ce monitoring permanent offre une visibilité précise sur l'évolution de l'état des machines au fil du temps. Les données collectées sont analysées pour identifier les tendances et anticiper les besoins de maintenance avant qu'une défaillance ne survienne. Cette approche proactive permet d'intervenir au moment optimal, évitant ainsi les dommages collatéraux causés par une panne soudaine. Le suivi régulier contribue également à maintenir les performances des équipements à leur niveau nominal, limitant les pertes d'efficacité liées à l'usure progressive des composants.
Remplacement préventif des pièces d'usure
Dans le cadre du MCO, le remplacement des pièces d'usure s'effectue de manière préventive, selon des intervalles définis par l'analyse des données historiques et les recommandations des fabricants. Cette stratégie permet d'éviter les défaillances en cascade provoquées par la rupture d'un composant critique. En remplaçant les pièces avant qu'elles n'atteignent leur limite de fatigue, on préserve l'intégrité globale de l'équipement et on réduit les contraintes mécaniques subies par les autres composants. Le remplacement préventif s'accompagne généralement d'une inspection approfondie des zones adjacentes, permettant de détecter d'éventuelles anomalies non visibles en fonctionnement normal. Cette approche systématique contribue à maintenir l'équipement dans un état proche de ses conditions initiales, prolongeant ainsi sa durée de vie utile.
Réduction de l'usure prématurée des composants
Le MCO intègre des techniques visant à réduire l'usure prématurée des composants mécaniques et électroniques. L'analyse des conditions de fonctionnement permet d'identifier les facteurs accélérant la dégradation des équipements, tels que les vibrations excessives, les surcharges ou les variations de température. Des actions correctives sont alors mises en place pour optimiser les paramètres d'exploitation et minimiser les contraintes subies par les matériels. La lubrification adaptée, le réglage précis des alignements ou encore l'équilibrage des pièces en rotation font partie des opérations de maintenance préventive qui contribuent à ralentir l'usure des composants. Par ailleurs, la formation des opérateurs aux bonnes pratiques d'utilisation des équipements permet de limiter les erreurs de manipulation susceptibles d'engendrer une usure prématurée. Cette approche globale, combinant optimisation technique et sensibilisation des utilisateurs, permet de préserver durablement l'intégrité des installations industrielles.
Meilleure maîtrise des risques opérationnels
La mise en place d'une stratégie de maintenance en condition opérationnelle contribue significativement à améliorer la maîtrise des risques opérationnels au sein des entreprises industrielles. En effet, le MCO offre une visibilité accrue sur l'état des équipements et leur évolution dans le temps, permettant ainsi d'anticiper les défaillances potentielles et leurs conséquences sur l'activité. Cette approche proactive de la gestion des risques s'appuie sur une collecte et une analyse systématique des données de maintenance, offrant une base solide pour la prise de décision. Les responsables opérationnels disposent ainsi d'informations fiables pour évaluer les risques liés à l'utilisation des équipements et mettre en place des mesures préventives adaptées. Le MCO facilite également la mise en conformité avec les réglementations en vigueur, en assurant une traçabilité complète des opérations de maintenance et des contrôles réglementaires.
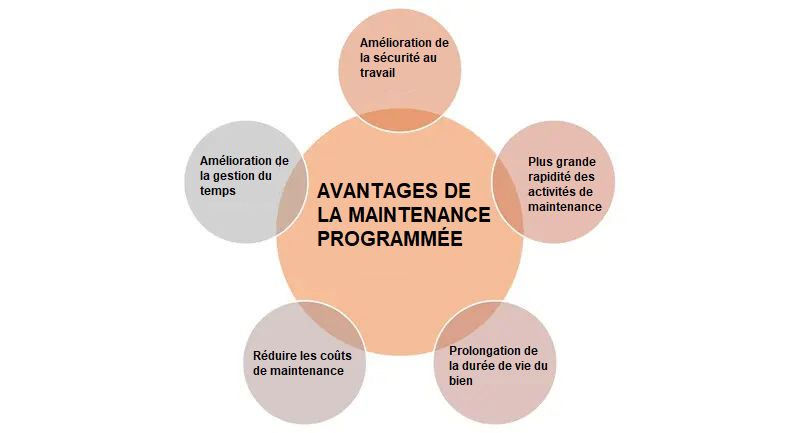
La réduction des arrêts non planifiés, rendue possible par le MCO, permet de limiter les impacts financiers et opérationnels liés aux pannes inopinées. Cette stabilité accrue de la production contribue à renforcer la confiance des clients et des partenaires commerciaux, préservant ainsi la réputation de l'entreprise. Par ailleurs, l'optimisation de la gestion des stocks de pièces détachées dans le cadre du MCO réduit les risques de rupture d'approvisionnement susceptibles de paralyser la production. La standardisation des procédures de maintenance et la formation continue des équipes techniques permettent quant à elles de minimiser les risques d'erreurs humaines lors des interventions. Enfin, l'approche systémique du MCO favorise une meilleure coordination entre les différents services de l'entreprise (production, maintenance, qualité, sécurité), contribuant ainsi à une gestion plus efficace et transversale des risques opérationnels.